A multikilowatt diode laser system that’s bright enough to cut and weld — even through a half-inch of steel — at greater efficiencies than today’s industrial lasers is being commercialized by MIT Lincoln Laboratory spinout TeraDiode.
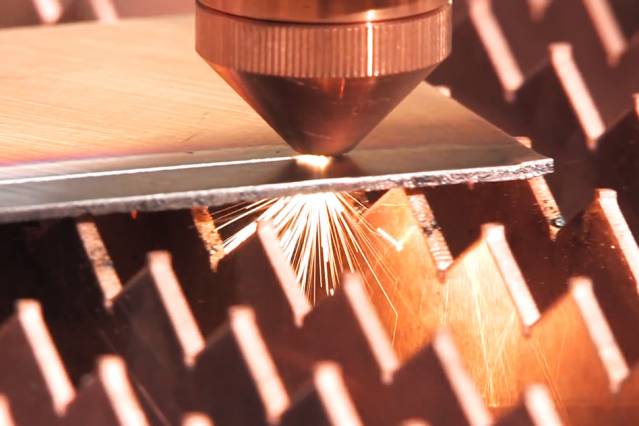
The 4-kilowatt TeraBlade runs on a novel power-scaling technique developed at MIT that manipulates individual diode laser beams into a single output ray. This allows for boosting power of a diode laser, while preserving a very focused beam.
“[The TeraBlade] has comparable beam quality as compared with traditional manufacturing lasers, such as carbon dioxide, disk, and fiber,” says TeraDiode co-founder and vice president Robin Huang, a former Lincoln Laboratory researcher and TeraBlade co-inventor. “However, because the TeraBlade is a direct-diode laser, it has the highest efficiency and lowest cost of ownership as compared with these other lasers.”
Huang says TeraBlade represents a “third generation” of industrial lasers. The first generation, which evolved a few decades ago, was carbon dioxide lasers, in which electricity runs through a gas to produce light. These are very bright, but can be as large as trucks and operate at about 20 percent efficiency.
Then came diode-pumped solid-state (DPSS) lasers — including disk and fiber — that first transfer energy from diode lasers into a medium, usually a crystal, before converting it into a laser beam. These operate only up to about 30 percent efficiency.
But the TeraBlade, aptly called a “direct-diode” laser, uses light directly from the diodes, skipping the DPSS conversion step and saving energy, Huang says. This means the TeraBlade operates with just as much power and brightness as all other industrial lasers — about 2,600 megawatts per square centimeter per steradian — at roughly 40 percent efficiency.
http://newsoffice.mit.edu/2014/startup-teradiode-invents-direct-diode-laser-bright-enough-to-cut-weld-0723